I’ve been changing tires for a few years now. I’m probably someone who shouldn’t waste my time, but ever since I swore I would never set foot in local motorcycle shop again I’ve been on a learn to change tire’s crusade. The past couple of years I’ve been working with a Harbor Freight motorcycle changer trying to make a bar that works efficiently. Inevitably I wind up giving up and using tire irons. I get the tires changed but by the end of the day I’m cursing never again. Recently I’ve been working with a duck head on a bar. My very limited strength seemed to be going mostly toward pulling the duck head out. After that experience I came up with some really cheap easy ways to improve both the harbor freight changer and convert it to a manual duck head machine. I’ll try and explain with pictures as follows, but I’m also looking for input as I noticed an old VRCC thread indicating a number of members are years ahead of me.
I’m really optimistic about this prototype but I don’t plan to use it until April or May when I do the front tire. I plan to have both disks and wheel bearings installed when I change the tire even though I’ll be changing out the 26 year old bearings. My wife’s take is you were really optimistic the last 4 times too. If you look at the pictures it will become very obvious that I can’t weld. Once I’m happy with the modifications I could always take it to my neighbor.
Tire machine changes: To fix the fact that the holes for the 2 stationary feet never allow my wheels to center, I remove the clevis pins completely. Then I use the adjustable clamping foot to center the wheel. Next I ratchet strap around all 3 feet to bring the 2 loose clamps in to clamp the wheel. The feet lean out and try to push the wheel up as opposed to clamping so I cinch the wheel down at each changer arm which also keeps the wheel from rotating. I got cheap 3m furniture glide material to protect the wheel. The cinch down also holds the tire off the lower bead (as the feet stick up into the tire) so you only have to worry about tire ride up the upper bead. I deal with the center bar being too wide to go through the wheel bearings by tuning it upside down IE hollow side down, threaded side up. I have a 3/8” x12” threaded nipple that goes through the bearings into the hole in the center of the changer and center bar. I have 3/8” brass caps on both ends of the nipple that I rounded with a grinder for a snug fit. One of the really cool parts is the bar slides up and down until you lock it in place up top so it becomes the height adjustment for the duck head. No modification required.
If you don’t have space or money for a tire changer I would think you could try mounting a 3/8” threaded flange to a ¾” piece of plywood, then 3/8” x12” nipple possibly bell reducer up to a ¾” pipe nipple for your bar rotation center. Maybe have holes for cinch straps and plywood stand offs to keep the tire and wheel up.
Duck head changes: I wanted a center rotation adjustable machine as I didn’t want to have to pivot the head for wheel size. Did I mention I can’t weld; so complicated fabrication is out of the question? I welded 4 pieces of 1” 16 ga sq tube together leaving a slide area to compensate for all my wheels. I had to make the center slot slightly wide with shims as the HF center bar is slightly wider than the square tube. 1” split collars and washers work great for the HF center bar, completing the duck head vertical adjustment / rotation bearing. I use ¾” sq tube slides for the duck head horizontal adjustment with plastic end caps at the bearing points. The slide bars are locked in place by 3/8” bolts with nuts welded to the mount / demount bar. I have a big tire iron in the 1” bar at the head showing that I’ll be able to shift my rotation leverage to the head if I need to push on the tire with the head hung up.
I’m also looking to change 12” trailer tires. Does anyone have any recommendations on small wheel heads?
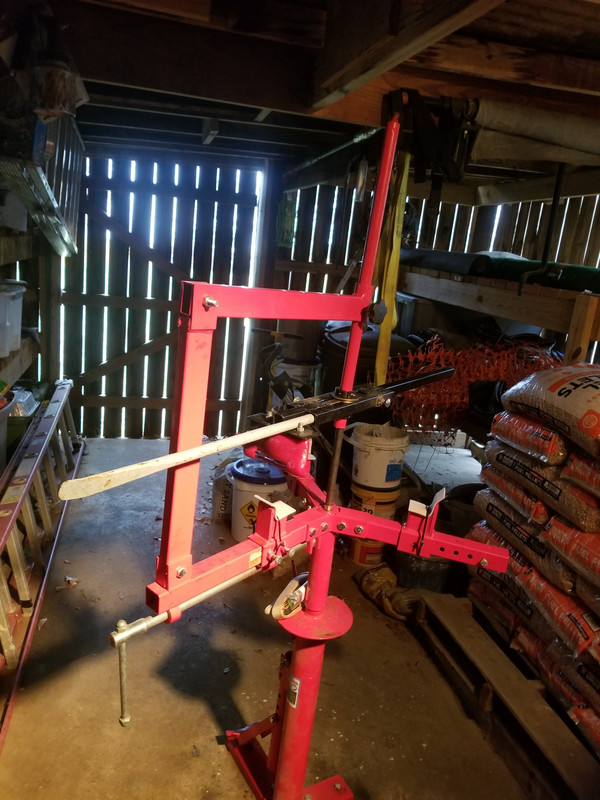
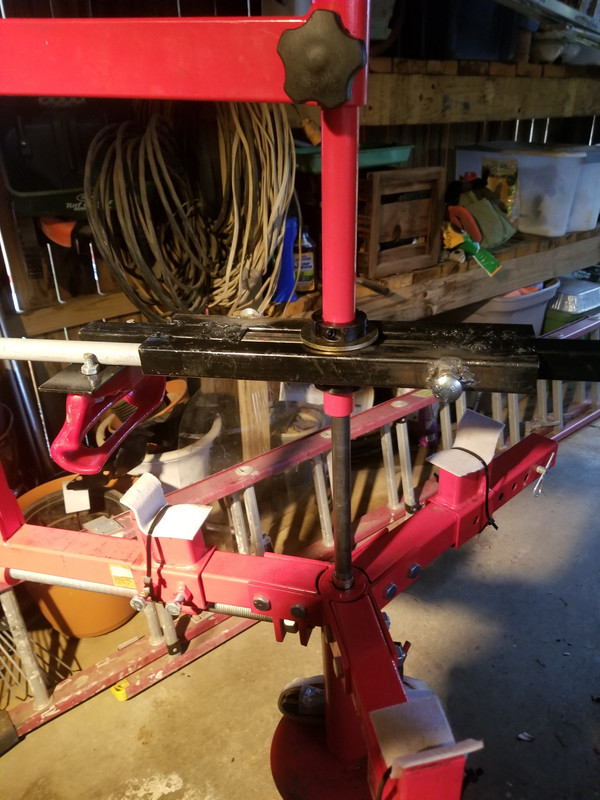
The attached video is really good! The presenter probably has a business that justifies him buying so many kits to come up with one system that works. This is definitely the more professional way to go!
https://www.youtube.com/watch?v=0GUHrOox5W8